Mastering the Art of 3D Printing: A Comprehensive Guide for Tech Enthusiasts
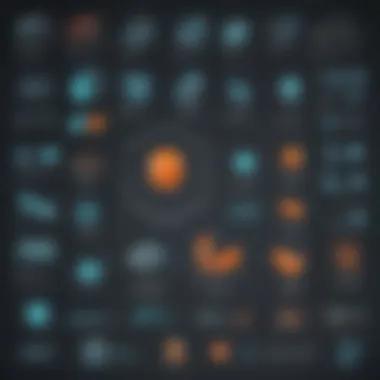

Overview of 3D Printing Process
In this section, we will delve into the complex yet fascinating world of 3D printing. From understanding the basic concepts to exploring advanced techniques, this guide aims to equip IT professionals and tech enthusiasts with valuable insights into additive manufacturing technology.
Understanding the Basics
We will start by unraveling the foundational principles of 3D printing, including the process of creating three-dimensional objects layer by layer. By grasping the key components involved in this innovative manufacturing technique, readers will gain a deeper appreciation for the intricacies of the printing process.
Exploring Advanced Techniques
For those seeking to expand their knowledge, we will also touch upon advanced techniques in 3D printing. From intricate design capabilities to enhanced material options, this section will shed light on the cutting-edge advancements shaping the future of additive manufacturing.
Importance for IT Professionals and Tech Enthusiasts
By the end of this section, readers will have a solid foundation in the 3D printing process, paving the way for a deeper exploration of hardware, software, and innovative trends in the industry.
Introduction
3D printing has revolutionized the world of technology, offering a unique approach to manufacturing objects with precision and customization. In this comprehensive guide, we delve into the intricate process of 3D printing, catering to IT professionals and tech enthusiasts seeking to expand their knowledge in additive manufacturing. By exploring the fundamental aspects and advanced techniques, readers will uncover the multifaceted realm of 3D printing.
What is 3D Printing?
At its core, 3D printing, also known as additive manufacturing, is a groundbreaking technology that enables the creation of three-dimensional objects through a layer-by-layer printing process. Unlike traditional subtractive manufacturing methods, which involve cutting and drilling material to shape an object, 3D printing builds up layers of material based on a digital design. This precise and efficient process allows for intricate geometries and customized designs that were previously challenging to achieve.
Importance of 3D Printing in Technology
The significance of 3D printing in technology lies in its ability to streamline prototyping, manufacturing, and customization processes. By harnessing the power of 3D printing, industries can rapidly develop prototypes, iterate designs, and bring products to market quicker than ever before. This technology empowers designers and engineers to visualize concepts in a tangible form, accelerating innovation and pushing the boundaries of what is possible in various fields, from aerospace to healthcare.
Applications of 3D Printing
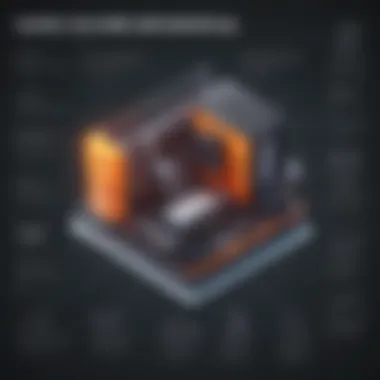

The applications of 3D printing are diverse and far-reaching, permeating various sectors with its versatility and efficiency. In healthcare, 3D printing aids in creating patient-specific implants, prosthetics, and anatomical models for surgical planning. The automotive industry utilizes 3D printing for prototyping parts and developing lightweight components to enhance vehicle performance. Moreover, architecture benefits from 3D printing to construct intricate models and architectural elements with precision. These applications merely scratch the surface of how 3D printing continues to transform industries and drive innovation across the globe.
Understanding the 3D Printing Process
Understanding the 3D Printing Process plays a pivotal role in this in-depth article on 3D printing. As the foundation of the entire additive manufacturing process, understanding how to navigate each step ensures a successful outcome. From designing the 3D model to the final printing of the object, each phase requires precision and comprehension. The intricacies of 3D printing, such as material selection, printer specifications, and slicing techniques, are demystified through a comprehensive breakdown in this section.
Step 1: Designing the 3D Model
Designing the 3D model serves as the starting point on the additive manufacturing journey. It involves translating ideas into digital blueprints that 3D printers can interpret layer by layer. Attention to detail, precision, and spatial awareness are key factors that determine the success of the final print. Factors like geometric complexity, structural integrity, and support considerations must all be factored into the design process to ensure a flawless end result.
Step 2: Choosing the Right 3D Printer
Selecting the appropriate 3D printer for a project is a critical decision. Various types of 3D printers cater to different needs, from Fused Deposition Modeling (FDM) to Stereolithography (SLA) machines. Considerations such as printing speed, layer resolution, build volume, and filament compatibility must align with the intended application. Understanding the strengths and limitations of each printer type is essential in achieving the desired print quality.
Step 3: Material Selection
The choice of material impacts the durability, aesthetic appeal, and functional properties of the printed object. Factors like mechanical strength, heat resistance, flexibility, and finish determine the suitability of a material for a specific application. Navigating through a myriad of options, including PLA, ABS, PETG, and exotic filaments, requires an understanding of their unique properties and behavior during the printing process.
Step 4: Slicing the Model
Understanding Layer Height
Layer height refers to the thickness of each deposited layer of filament during printing. This parameter influences the surface finish, detail resolution, and overall print time. Selecting an optimal layer height balance between print quality and speed is crucial. Lower layer heights offer finer details but extend printing duration, while taller layers expedite printing but may compromise detail.
Optimizing Printing Speed
Printing speed directly impacts production efficiency and part quality. Finding the right balance between speed and print accuracy is essential for achieving optimal results. Factors such as printer capabilities, material properties, and part complexity influence the speed settings. Fine-tuning the printing speed helps in reducing print time without sacrificing print quality or structural integrity.
Step 5: Printing the Object
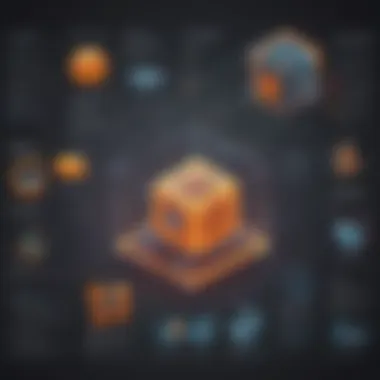

The final step in the 3D printing process involves bringing the digital model to life. Monitoring the print progress, ensuring proper bed adhesion, and addressing any issues that arise during printing are crucial for a successful outcome. The culmination of meticulous design, material selection, and slicing strategies results in a tangible object that exemplifies the potential of additive manufacturing technology.
Advanced Techniques in 3D Printing
In the realm of 3D printing, mastering advanced techniques elevates enthusiasts from novices to virtuosos in additive manufacturing. This section delves into the intricacies of advanced techniques within the 3D printing process, providing readers with a nuanced understanding of the subject matter. Embracing advanced techniques empowers individuals to explore the full potential of their 3D printers, pushing boundaries and enhancing the complexity of printed objects.
Multi-material Printing
Multi-material printing stands as a pinnacle of innovation in the 3D printing world. This cutting-edge technique allows creators to fabricate objects using a combination of different materials, enabling the production of intricate designs with varying properties. By seamlessly integrating various materials during the printing process, multi-material printing opens doors to limitless creativity and functional versatility. Whether creating prototypes with diverse characteristics or artistic pieces with contrasting textures, the ability to print with multiple materials expands possibilities in additive manufacturing.
Support Structures and Rafts
Support structures and rafts serve as the unsung heroes of successful 3D prints. These elements play a crucial role in maintaining the structural integrity of complex designs, preventing deformities and ensuring the accuracy of printed objects. By strategically implementing support structures and rafts, creators can conquer challenging geometries and achieve flawless results. Understanding the significance of support structures and rafts is vital for optimizing print quality and overcoming obstacles inherent to 3D printing.
Post-Processing and Finishing
Sanding and Smoothing
Post-processing techniques like sanding and smoothing bring refinement and polish to 3D printed objects. Sanding removes layer lines and imperfections, resulting in a seamless surface finish, while smoothing enhances the tactile quality of prints. The meticulous process of sanding and smoothing transforms rough prototypes into sleek, professional-grade products, ready for display or functional use. Despite requiring time and precision, the benefits of sanding and smoothing are undeniable, enhancing the visual appeal and performance of 3D printed creations.
Painting and Surface Treatments
Painting and surface treatments offer a creative palette for customizing 3D prints with vibrant colors and unique finishes. This aspect of post-processing allows individuals to add personal flair to their creations, transforming them into bespoke artworks or market-ready products. Whether applying intricate details with brush strokes or experimenting with specialized coatings, painting and surface treatments provide endless opportunities for artistic expression in the realm of 3D printing.
Overhangs and Bridging
Navigating the challenges posed by overhangs and bridging is a test of a 3D printer's capabilities and an operator's expertise. Overcoming these obstacles requires precise calibration, support adjustments, and strategic planning during the slicing process. Mastering the art of addressing overhangs and bridging not only ensures the structural integrity of prints but also demonstrates a mastery of nuanced printing techniques. By conquering overhangs and bridging challenges, creators can unlock new design possibilities and elevate the quality of their 3D printed creations.
Troubleshooting Common Issues
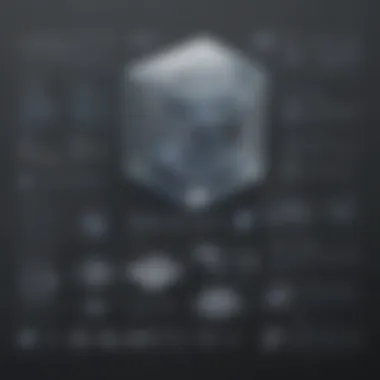

Troubleshooting common issues in the 3D printing process holds paramount importance in this exhaustive guide. Addressing and rectifying these issues ensures a smooth and successful additive manufacturing experience. By delving into the intricacies of troubleshooting, readers can overcome obstacles that may hinder the creation of high-quality printed objects. Attention to detail in identifying and resolving common issues guarantees efficiency and precision in the 3D printing workflow. Proper troubleshooting enhances the overall understanding of 3D printing and empowers individuals to tackle challenges with confidence.
Warpage and Adhesion Problems
Warpage and adhesion problems are prevalent issues that can affect the quality of 3D prints. Warping occurs when the printed object's corners lift or curl, leading to structural deformities. Adhesion problems result in poor bonding between layers, compromising the object's strength and integrity. Understanding the causes of warping and adhesion issues, such as inadequate bed leveling or improper print settings, is crucial for effective troubleshooting. Implementing solutions like adjusting print temperatures or using specialized bed adhesives can mitigate warping and adhesion problems, ensuring seamless printing processes.
Layer Separation Issues
Layer separation issues, where printed layers do not adhere properly, can result in fragile and brittle objects. Factors such as insufficient extrusion or nozzle clogging contribute to layer separation challenges. Resolving these issues demands meticulous recalibration of printing parameters and thorough cleaning of extruder components. By diagnosing and addressing layer separation issues promptly, individuals can produce solid and durable 3D prints with enhanced layer adhesion and structural strength.
Print Quality Defects
Print quality defects encompass various imperfections that diminish the visual appeal and structural integrity of 3D printed objects. Stringing, characterized by thin strands of material between printed sections, detracts from the object's smooth finish. Blobs and zits manifest as irregularities on the print surface, compromising its overall quality. Identifying and rectifying these defects involves adjusting retraction settings, optimizing print speeds, and fine-tuning cooling mechanisms. Overcoming print quality defects through precise troubleshooting enhances the aesthetic value and functionality of 3D printed creations.
Stringing
Stringing, a common print quality defect, results in unsightly threads of material between print features. Despite its prevalence, stringing can be effectively managed through meticulous calibration of retraction settings and nozzle temperatures. By fine-tuning these parameters, individuals can minimize stringing issues, resulting in cleaner and more accurate prints. While stringing may initially pose challenges, mastering its mitigation techniques elevates the printing standard and overall output quality.
Blobs and Zits
Blobs and zits present as irregular surface blemishes on 3D printed objects, tarnishing their visual appeal. These defects arise due to filament oozing or accumulation during the printing process, leading to extraneous protrusions. Addressing blobs and zits entails refining print cooling settings, adjusting layer heights, and optimizing extrusion rates. Focused efforts on eliminating blobs and zits enhance print surface smoothness and overall geometric precision, contributing to the production of flawless 3D prints.
Safety Precautions and Best Practices
In the realm of 3D printing, adherence to safety precautions and best practices is of paramount importance. Properly implementing these measures not only ensures a secure working environment but also maximizes the efficiency and longevity of your equipment. Safety precautions encompass various aspects, including ventilation, fire safety, and maintenance procedures. Ventilation and filtration are particularly crucial to mitigate the potential risks associated with fumes and particulate matter generated during the printing process. By maintaining good ventilation, you can safeguard against inhaling harmful emissions and enhance air quality in the vicinity of the printer. Adequate filtration systems further help in containing pollutants, promoting a healthier workspace free from airborne contaminants. Incorporating these practices minimizes health hazards and contributes to a more sustainable working environment.
Ventilation and Filtration
Ventilation and filtration mechanisms form the cornerstone of a safe and efficient 3D printing setup. Effective ventilation involves the proper circulation of air to dissipate volatile organic compounds (VOCs) and other airborne particles emitted during the printing process. Implementing a ventilation system that directs fumes away from the workspace helps in preventing exposure to potentially hazardous substances. Additionally, utilizing filters designed to capture and eliminate harmful particles enhances air quality and reduces health risks for individuals operating the printer. By prioritizing ventilation and filtration, you not only safeguard personal well-being but also promote a cleaner and safer work environment conducive to optimal printing outcomes.
Fire Safety Measures
When engaging in 3D printing activities, it is imperative to institute adequate fire safety measures to mitigate the risk of fire accidents. Utilizing fire-resistant materials for construction, such as fire-retardant filament, and investing in fire extinguishers in the vicinity of the printer are foundational precautions to prevent and combat fires effectively. Implementing fire safety protocols and conducting regular fire drills contribute to preparedness and swift response in case of emergencies. Additionally, maintaining a clear and uncluttered workspace minimizes fire hazards and facilitates safe evacuation if required. By prioritizing fire safety measures, you establish a secure operational environment that prioritizes well-being and minimizes potential risks.
Maintenance and Calibration
Maintaining and calibrating your 3D printer regularly is essential for ensuring consistent performance and prolonging its lifespan. Regular maintenance tasks, including cleaning the extruder, lubricating moving parts, and inspecting for wear and tear, help in preventing unexpected breakdowns and malfunctions. Calibration adjustments to settings such as bed leveling and extrusion rates ensure accurate printing and high-quality output. Prioritizing a structured maintenance schedule and adhering to calibration protocols guarantee optimal printer functionality and longevity. By dedicating time to maintenance and calibration efforts, you uphold the efficiency of your equipment and uphold the standards of quality output in your 3D printing endeavors.